Anyone involved in infrastructure development will intuitively understand the value of road base. This material is an essential foundation for any extensively paved surface, including highways, driveways, and everything in between.
What Is The Purpose Of Road Base In Infrastructure Development?
Road base has multiple roles in infrastructure development, ensuring contractors can complete projects to clients’ specifications. The material has properties that make it non-negotiable for practically all transportation construction projects.
1. Drainage Management
Road base plays a critical role in drainage management, helping to guide stormwater away from material subgrades that can lead to damage. Road base channels water into surrounding areas to prevent heavy rainfall from affecting the position of the road’s surface
Without proper drainage management, roads can subside or develop extensive cracking. Some road segments can fall away along with saturated land in steep areas.
2. Load Distribution
Road base also assists in load distribution – or the ability of roadways to spread weight from vehicles over a larger surface area. This property is essential for maintaining road surfaces long-term. Sections of roads under excessive pressure from heavy goods vehicles can undergo extensive damage when underlying soil becomes excessively compressed. Road base prevents this process from playing out as rapidly by shifting weight support laterally.
3. Improved Pavement Surface
Highways, streets and driveways with road bases also benefit from improved pavement surfaces. Roads remain closer to their intended specification for longer and exhibit fewer deformations, settlements and rutting.
This feature is valuable in long-term infrastructure projects such as new road developments. Public sector clients want long-term returns on their investments and value for taxpayer money. Quality road surfaces enable new installations to last decades with less intermittent maintenance.
4. Ride Smoothness
Another purpose of road bases is to improve ride smoothness for vehicles. The subbase reduces surface anomalies, making the road experience more pleasant for cars, vans, and trucks.
The improved smoothness comes from a reduction in pavement irregularities. Applying road base in infrastructure projects improves the contractor’s ability to provide an efficient and safe surface.
5. Reduction In Soil Instability
Civil engineers and contractors also install road base to maintain soil stability. Adding aggregates to the sub-layers of roads can improve soil quality and make it more capable of accommodating heavy vehicles.
Reinforcement works by mixing road base with poor-quality subgrades or clay. The aggregate improves the overall performance of the soil, shoring it up to carry heavier loads.
6. Weathering Resistance
Another purpose of road base is to improve a pavement’s weathering resistance in cold climates. Crushed granite and limestone provide insulation that improves the road’s resistance to freeze-thaw weathering. It can also reduce instances of frost heave, where water penetrates into the ground and undergoes volumetric expansion as temperatures drop below zero.
7. Greater Sustainability
Infrastructure developers also use road base to reduce the environmental impact of new road building. Instead of applying fresh asphalt, many contractors and civil engineers recycle and reuse existing resources, reducing the need for virgin material extraction. This approach helps to reduce CO2 emissions and damage to the natural environment from excessive quarrying and extraction.
8. Risk Mitigation
Finally, road base is a critical tool for risk mitigation on infrastructure projects. It reduces the damage done to road surfaces by soil settlement and potholes.
Again, it does this by spreading the load of vehicles and providing a subsurface for smoother repairs. Engineers can quickly fill in cracks and damaged road sections instead of managing problematic subsoil.
Types Of Road Base Materials
Various road base materials exist for infrastructure development. The choice of which to use depends on your budget, use case, weather conditions, and material availability. Some road base materials may not suit your application.
Crushed Stone
Crushed stone is one of the top road base material choices. Engineers love using it because of its natural ability to spread loads and reduce pressure on subsoil.
The crushed stone ranges from tiny grains to significantly larger particles. Most engineers use a blend of particle sizes to provide road surfaces with the desired qualities.
Crushed stone can also be an eco-friendly option. Recycled stone is easy to obtain and performs similarly to virgin stone extracted from mines.
Gravel
Gravel is another road base option for developers looking for an affordable option. Engineers like this material because it offers excellent drainage, preventing pools of water from forming on the surface.
However, gravel can be ineffective as a base for some soil types. Furthermore, it may not provide as robust a base as unweathered rock.
Crushed Rock Fines
Crushed rock fines are another option for developers looking to add inexpensive material to the road base. This type of rock forms a compacted layer under load, making it suitable for highways and other road surfaces expecting heavy vehicles.
Crushed rock fines are small particles of rock, sometimes called “quarry fines” in reference to their derivation from quarrying activities. Typically, engineers combine them with larger rock particles to create a more well-rounded road base with more features. These particles are not suitable for isolated use.
Engineered Fill
Engineered fill isn’t a separate material category. Instead, it refers to materials that achieve specific standards based on engineers’ desired specifications.
Engineered fill benefits from being tested for suitability in various infrastructure applications ahead of time. Contractors and builders can order material, knowing it is appropriate for their application, without worrying about road deformations, potholes, or any other consequences of a poorly chosen road base.
Crushed Limestone
Some regions also use crushed limestone as a road base if it is available in large, accessible volumes in the local area. The material has reasonable compaction qualities, making it suitable as a foundation for various road surfaces. However, it may lack the long-term performance of engineered fill.
Fibre-Reinforced Base
Fibre-reinforced base is another option made by combining synthetic and natural fibrous materials to reduce road surface cracking. Engineers use this material in infrastructure applications requiring high tensile strength.
Evidence suggests that fibre-reinforced base implementation reduces road surface cracking. Therefore, it may improve durability considerably beyond conventional approaches, which could explain why it is becoming more popular.
Geogrids
Finally, some engineers opt for fully synthetic geogrids for road base layers. These plastic-derived materials can be highly effective at distributing load and preventing splitting or rutting of the road base.
Engineers typically use them when dealing with weak subsoil and need a solution that can spread weight more widely. The conventional approach is engineered filler, but geogrids can distribute force over a larger area. Typically, you find these road base options in clay soil areas where road compression is considerably more likely.
In summary, it should be clear by now why road base is essential. It offers structure support with load distribution and drainage management features. It also helps road surfaces last longer and provides drivers with a smoother driving surface.
How To Choose A Quality Road Base
Choosing the most suitable road base for your project requires a careful process. The following are some of the factors you’ll want to consider:
Your Project Requirements
First, you’ll want to think about what road base type is most suitable for your project. You’ll need to consider:
- The volume of traffic
- Its ability to bear heavy loads (and whether this is necessary)
- The material’s local availability
- The type of weathering and climate the infrastructure will experience
This part of the process requires researching each material and conducting a cost-benefit analysis to determine the most suitable. You will also need to consider the designed quality and capacity of the road you are building.
The Soil Type
The next step is to consider the soil type. The best soil for road construction is dense-graded soils with minimal air pockets. These varieties are less likely to compress over time and can interact more favourably with road base.
Quality soils also combine particles of all sizes. Poorer options requiring significant enrichment often have a large proportion of fines, though this might be okay if you are constructing simply gravel tracks.
You will need to evaluate the soil for quality and decide which type of enrichment to use. Softer soils will require additional road base to render them safe, while harder ones provide you with more freedom.
If you are concerned about particle size distribution and strength characteristics, choose graded or engineered options. You can adjust these depending on the strength and load distribution characteristics you need, based on the underlying soil type.
Material Quality
Once you choose a road base such as gravel or crushed stone, the next step is to consider the quality. Again, this involves checking whether the material has the correct physical properties in terms of:
- Compaction
- Strength
- Particle size
Combining particles from various sources can help improve the overall characteristics and reduce the need to compromise on these factors.
Availability Locally
Road base isn’t necessarily expensive to produce, but it takes a lot of energy to transport because of how heavy it is. A truckload of rock may only provide a thin layer of road base for a small section of a major highway.
For this reason, engineers often seek out local options to reduce costs and environmental impact. Road base sourced locally is often cheaper and doesn’t require drivers to transport it on the back of trucks over long distances.
Drainage
You’ll also want to consider the drainage characteristics of the road base. Areas receiving high volumes of rain may require a thicker layer of material under the asphalt road surfaces.
Suitable materials for drainage include gravel and crushed stone because they permit water to pass through easily. Denser options and sand may not be as suitable in areas receiving high rainfall.
Compaction And Thickness
Another consideration is compactness and thickness. You’ll need to ensure the material is sufficiently dense and thick to accommodate your infrastructure project’s needs.
Compaction is essential for ensuring the material has sufficient load-bearing characteristics. If road base isn’t compact, paved surfaces are at higher risk of rutting, potholing and collapse.
The thickness of the road base depends on various factors, such as soil quality and traffic volume. Softer soils often require additional reinforcement and larger volumes of material for safe road construction overhead. Climate can also be a factor, with engineers preferring thinner layering of material in areas prone to ice expansion heave.
Testing
Once you decide on a material to use and begin work, you’ll need to conduct testing to ensure the road base is suitable for the intended use. In some cases, you can follow established best practices for the local area already taking usage, soil quality and climate into account. However, you may need to implement bespoke arrangements, depending on the prevailing use case.
Various methods for testing a road base include:
- California Bearing Ratio (CBR), which involves measuring the road surface’s resistance to penetration using a standardised piston assembly
- Sieve analysis, which includes analysing the particle distribution in the road base, checking it meets the proper specifications
- The Proctor Compaction Test, which determines the optimal moisture content and dry density of the road base material
- The California Rut Test, which examines the road base material’s resistance to rutting in high-traffic areas
Cost-Benefit Analysis
Finally, you’ll want to conduct a cost-benefit analysis to help you choose the optimal material given your budget constraints. While some options offer superior performance, shipping them to the desired area may be infeasible for cost-related reasons. Moreover, the analysis may also reveal that some short-term options aren’t as good as long-term alternatives.
Where Can You Find Sustainable Road Base Options?
If you are looking for road base for an infrastructure project, Gravel Deliveries can help. We offer rocks, gravel, and aggregates for construction projects. Get premium materials delivered on time, every time, to your location, all facilitated by experienced delivery drivers who take every precaution to ensure that materials arrive at their destination at the specified time and in perfect condition. Gravel Deliveries can also help you answer your questions such as how to calculate the amount of gravel you need for your project or other questions you might have.
So what are you waiting for? Give our team a call and find out how we could help you get the road base you need for your infrastructure project.
We supply & deliver quarry and landscaping materials to a host of leading brands including
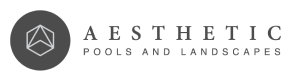
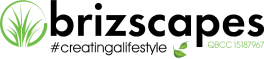
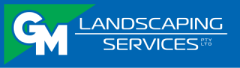